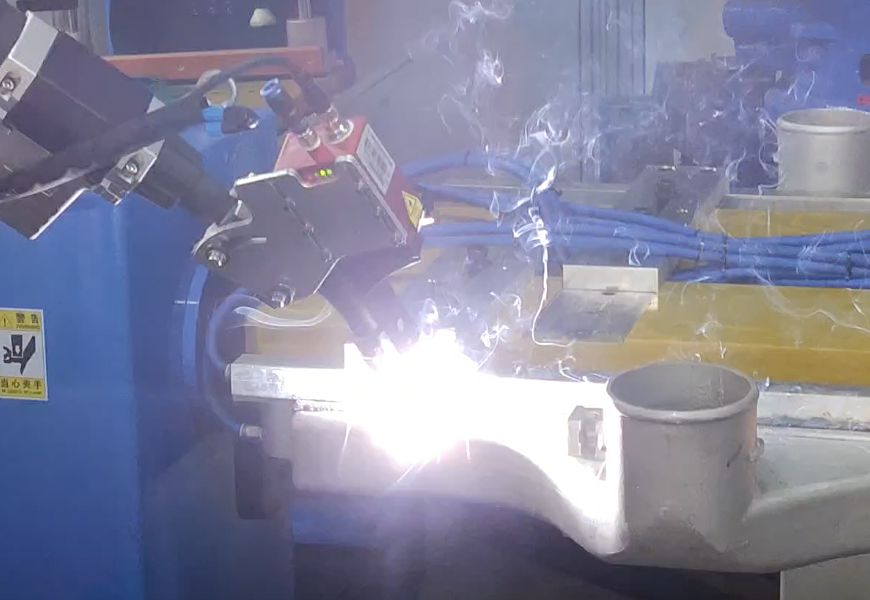
这代产品在专机系统有数十台的应用。在这过程我们发现,大部分工厂环境恶劣,分体式传感器不仅工控机成本高,体积大,而且是一个重大不稳定因素。
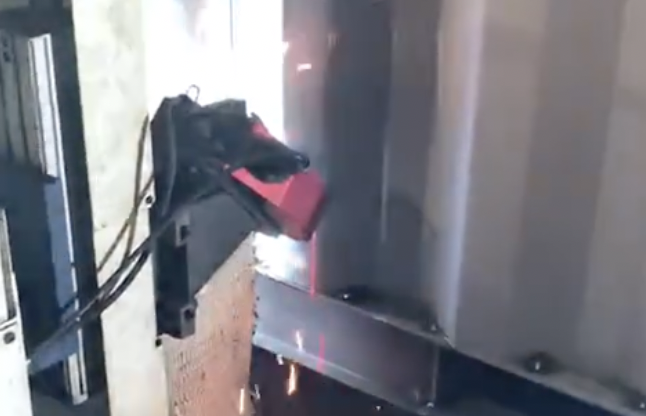
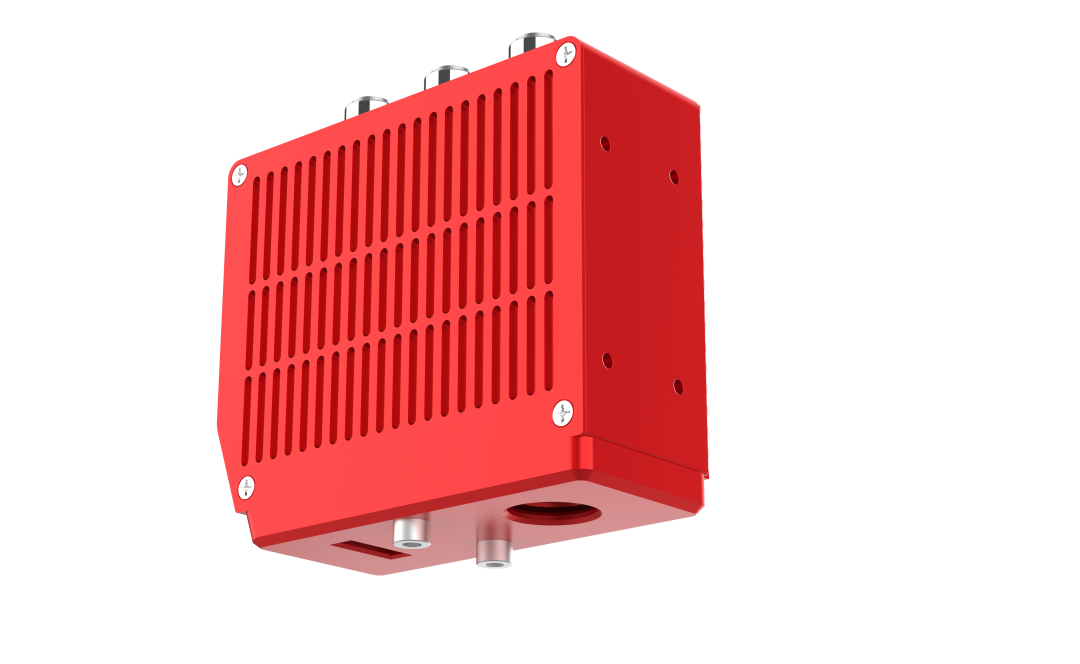
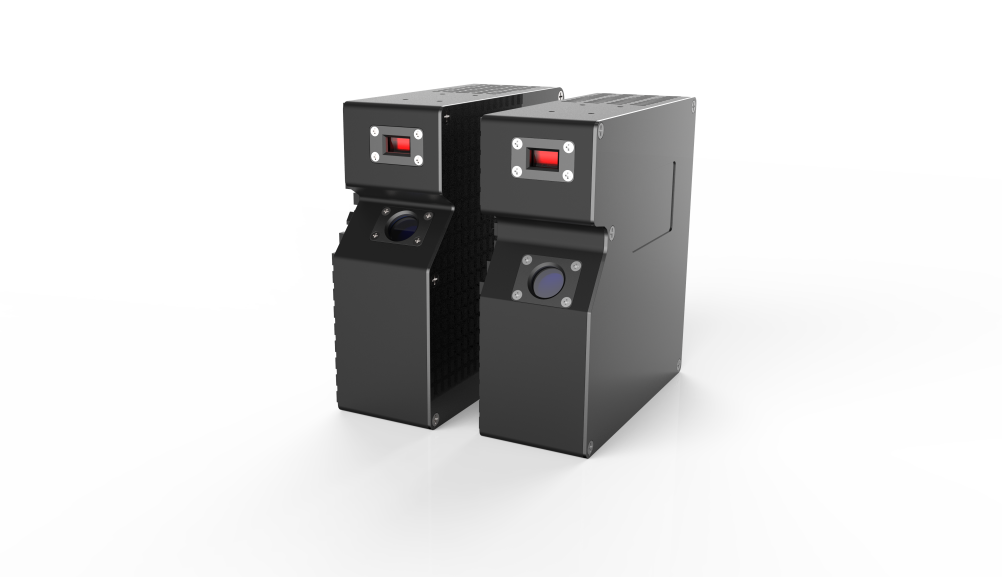
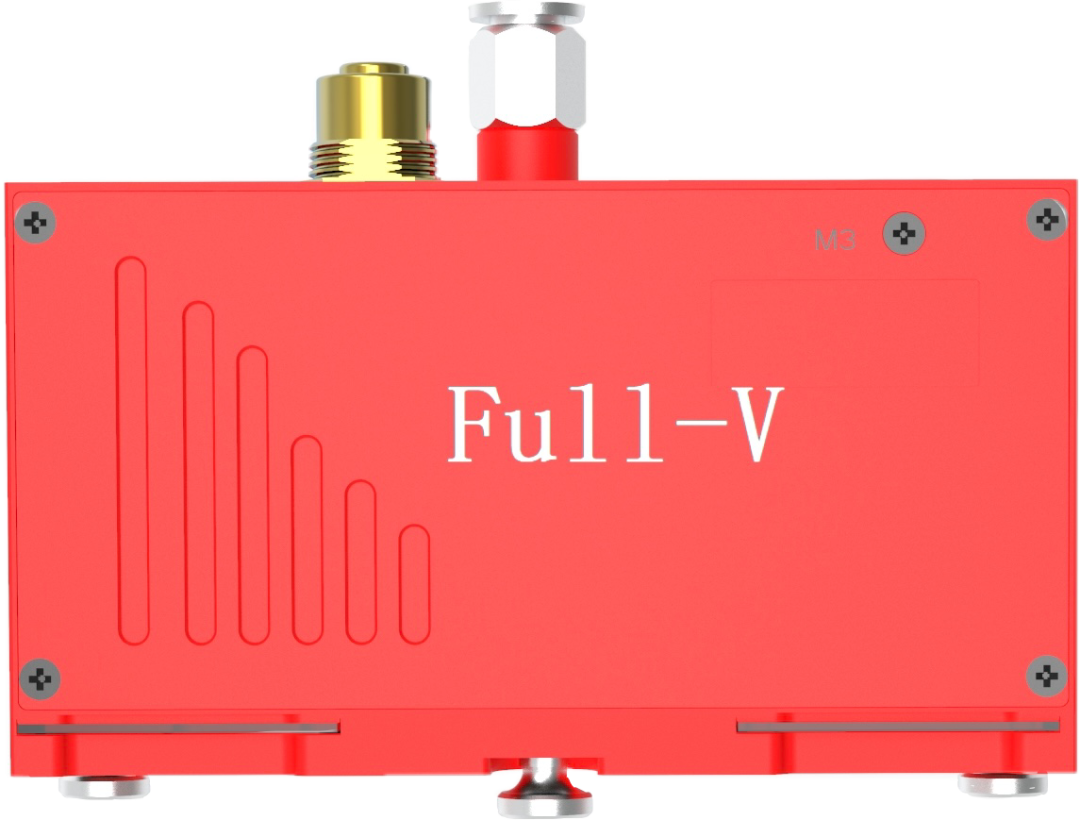
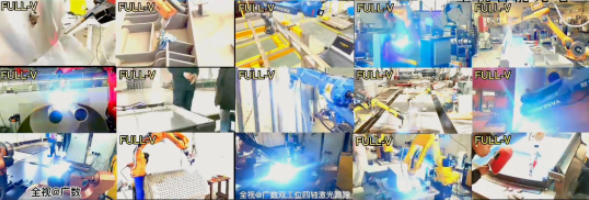
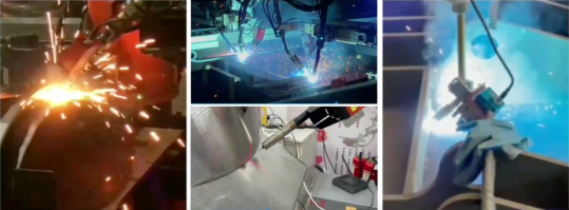
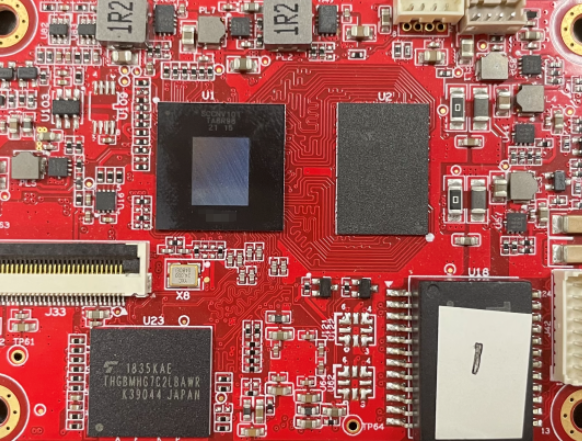
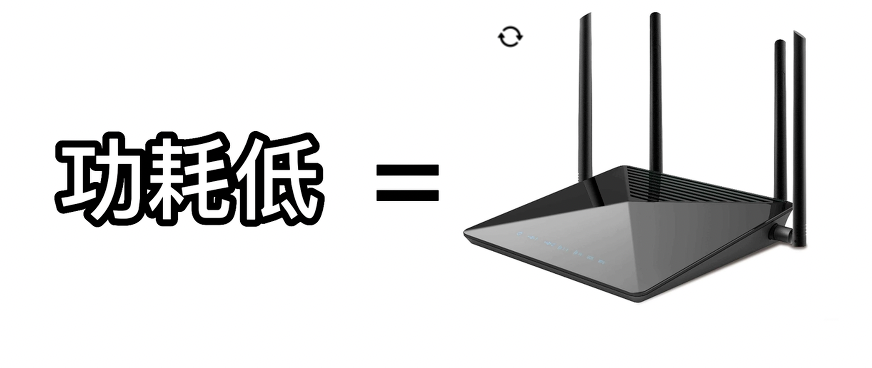
项目中总结发现,行业面临最大的问题是金属表面炫光、焊接过程中的飞溅弧光、焊点的检测、以及零缝隙的对接焊缝识别等。
这些行业难题都已经无法通过光学或物理方式得到解决,只能依赖于算法解决。
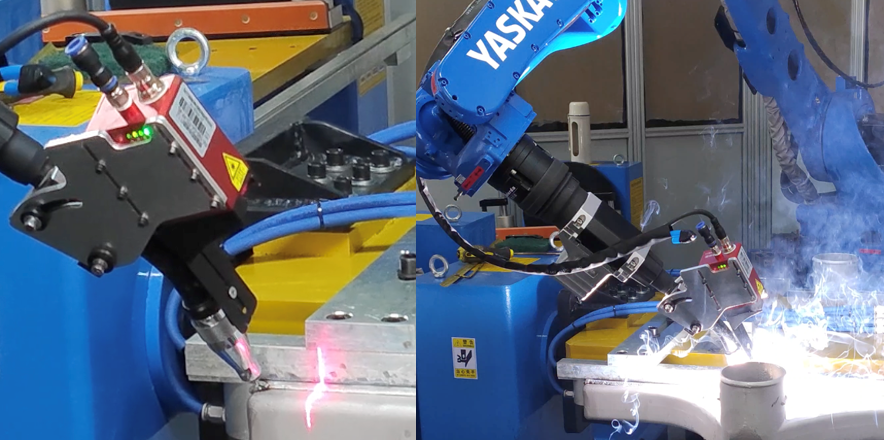
这就需要有经验的技术支持工程师,现场进行复杂的算法参数配置,这样会造成项目交付周期长,成功率低等风险。
因此第四代算法针对炫光淹没激光线、炫光与激光线相似等4种恶劣场景,实现全自动炫光消除算法。
弧光和飞溅在实时跟踪问题上又是一个巨大的挑战,弧光会淹没激光线、飞溅会打断激光线或与激光线非常接近,同时工件又在不停变化。传统的目标检测、目标跟踪算法在这种恶劣条件下都已经失效。
我们利用Sensor高达240HZ高速成像特性,采用空间超分算法重建激光线,以此消除炫光和飞溅的影响。
传统焊点检测主要通过激光线形状、面积等特征进行检测,对角焊缝效果比较好,但是对于对接、搭接、直线/圆弧等焊缝效果并不好。
通过对数据进行时间序列对比分析,并时域重建,精准检测出对接、搭接等焊缝类型上的焊点。
另一个具有挑战性的问题是薄板对接,其缝隙非常小,不仅缝隙会接近0,而且存在各种毛边干扰。对于这种0缝隙的对接焊缝我们定制了专用算法,不但能识别焊缝还能识别焊点。
最后就是高速扫描,通过传感器高速扫描工件,生成三维模型后,能自动生成焊接轨迹和工艺应用参数。这得益于240HZ高速图像采集和12核GPU,可达到每分钟6米的扫描速度。节拍上与3D拍照接近,但是精度更高,并且完全不受弧光、环境光干扰。适用性和可交付性更高。
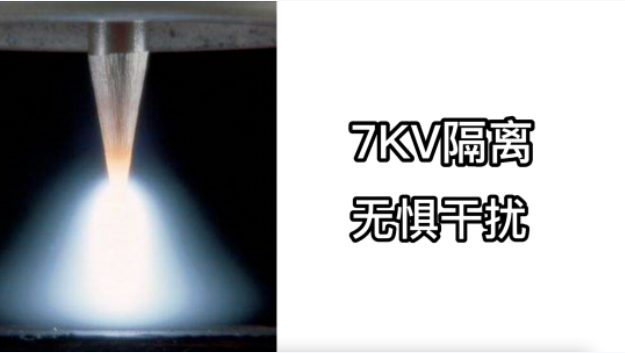
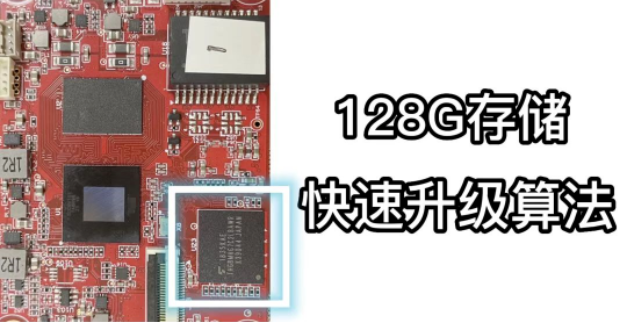
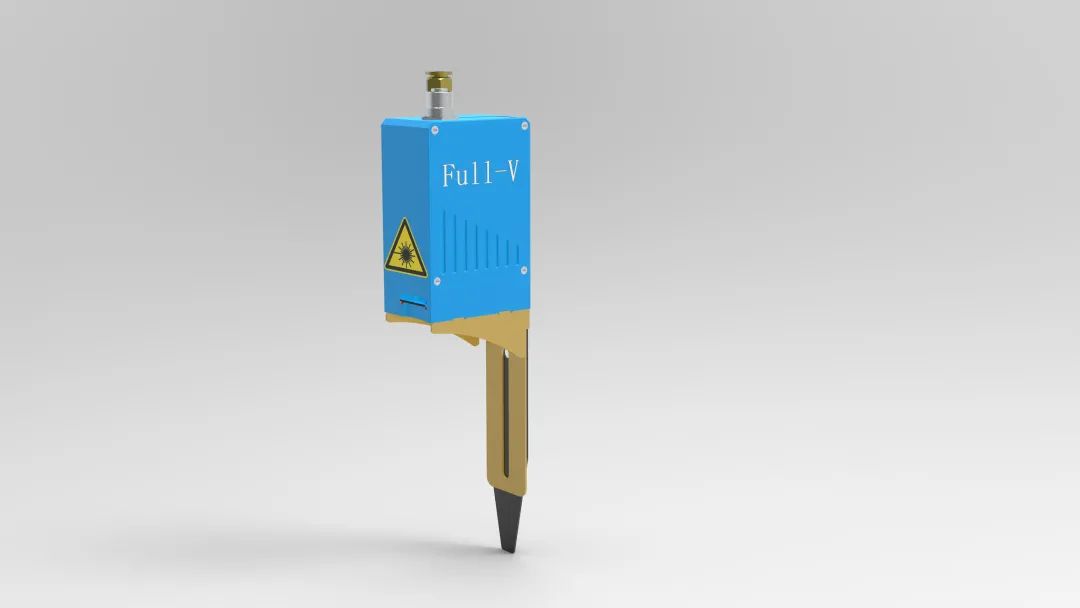